- Mechanical
- Steel
STLCutter 2 - Day 19
It's been about 30 months since I did some work on it, and I had been having discussions with another kit car manufacturer about buying it. GKD Sportscars, like Aeon Sportscars are based in Kent, and a few weeks ago, they'd moved the machine to their workshop a few miles away from Aeon's workshop - and it was a matter of negotiating the price.
Since it had been so long, and I hadn't been involved in the transfer, I was expecting a couple of days getting it back together again - mainly trying to find missing bolts.
When I arrived, I saw that the bed looked okay, but the beam was quite rusty. Peter (the owner of GKD) told me that Keith had kept the bed in the workshop, but the beam was under a cover outside.
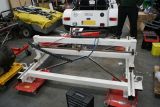
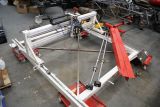
The first job was to get the beam running on the trains, and then the ball screws fitted, the motors fitted and finally the covers for the screws.
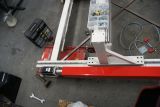
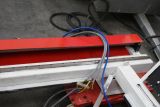
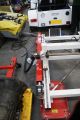
This was the first time I'd seen it with the red and white colour combinations, and it looks quite good - just a pity the white has got a bit dirty (but then I never got around to putting another coat on the machine).
I manually pushed the long axes and made sure that it all moved okay - and although the rust was making it a bit noisy, it still seemed okay.
So, the electrics were wired up. Some of the existing wiring was a bit dirty, so I had to trim down the wire and re-strip it, but it all went together.
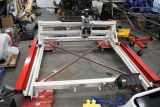
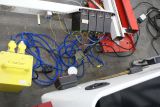
And then it was time for the big turn-on. We plugged it in and turned it on. It made all the same noises as before - and the torque of the motors was as good as it was before (there's no way I could manually move them with the contorllers turned on). I used a little test board I made to test it at Aeon's workshop, and was able to show the motors working.
This was good - I wasn't expecting to get this far today, and it meant everything was in place to actually use it.
Peter went back to his house to get a spare computer which he'd installed Mach 3 on, and after a lot of hassle, we got the computer running (something was causing it to randomly reboot - we didn't get to the bottom of it, but we were able to use it enough).
Getting Mach 3 to move the machine took a lot longer than expected - their default of 2000 steps per unit was a lot higher than my calculated 8 steps. I had forgotten that the controllers were doing half-stepping, so it was actually 16 steps for the X and Y axes, and 40 for the Z axis.
I also did a little bit of playing with the velocity and acceleration, and found that the machine's maximum speed was around 20 metres per minute - although occasionally it would stall, so we settled for 18 metres per minute, and an acceleration of 6 metres per minute per second (the Z axis has a different ball screw profile, so we set this to 6 metres per minute, and 2 metres per minute per second acceleration). This was exceptionally responsive, and looked good.
A very quick bit of gcode and we had a square cut into a block of foam:
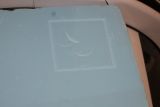
And after a bit of experimentation with the Z axis, we were able to cut a whole block out of the foam - and with the motor controlled by Mach 3.
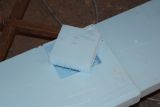
Unfortunately, I'd left the magents and reed switches for limit switches at home, so I'll need to pop back to fit them. And Peter would like me to research how to make a floating head, since he'd like to use it for plasma cutting.
Peter'll tidy up the wiring over time, and also put it on some longer legs so you don't need to bend over in order to move the work on and off the bed.
All in all, I'm surprised at how quickly we got it going again. Although perhaps I shouldn't have been - there really isn't that much to them.